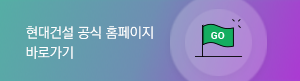
“도시의 미래가 지하로 향하고 있다(CNN 방송)”
빼곡한 건물, 각종 인프라로 가득한 지상을 벗어나 교통·물류 등 다양한 공간이 지하로 이동하고 있습니다. 세계적으로 지하 공간 개발에 대한 관심이 증가하고 있는 가운데, 이를 현실화할 때 꼭 필요한 기술 중 하나가 바로 TBM(Tunnel Boring Machine)입니다. TBM은 소음·진동에 강하고 안전한 친환경 공법으로 도심지 터널 굴착 공사에 적합한데요. 여기 국내 최대 단면 쉴드 TBM을 이용해 국내 최초로 한강 밑을 관통하는 도로터널을 짓는 현장이 있습니다. 바로 현대건설이 시공 중인 ‘고속국도 제400호선 김포~파주간 건설공사 제2공구’입니다.
글=이희정 / 사진=이슬기
“지름 14m, 길이 125m, 무게 3200톤에 달하는 터널 굴착기계, TBM(Tunnel Boring Machine)이 이제 한강 하부로 들어갈 준비를 마치고 굴진(掘進)을 시작합니다!”
지난해 12월 13일, ‘고속국도 제400호선 김포~파주간 건설공사 제2공구(이하, 김포~파주 2공구)’. 이날 현장에서는 본격적인 지하고속도로 건설의 서막을 알리는 굴진식이 열렸습니다. 행사에는 원희룡 국토교통부 장관을 비롯해 현대건설 윤영준 사장, 한국도로공사 김일환 사장 직무대행, 국토교통과학기술진흥원 박승기 원장 등이 참석해 자리를 빛냈는데요. 국내 최대 구경(口徑)이자 해외에서도 시공사례가 흔치 않은 규모인 까닭에 언론사들의 취재 열기도 뜨거웠습니다.
[ 고속국도 제400호선 김포~파주간 건설공사 2공구 현장에서 열린 굴진식 행사 전경. ]
TBM은 화약을 터뜨린 후 땅을 뚫는 보편적인 터널 시공 방식과 달리 거대한 강철 굴착기계를 이용해 터널을 만드는 선진 공법입니다. 최근 수도권광역급행철도(GTX) 등 도심지 지하 공간 개발에 TBM을 적용하기 위한 논의가 활발히 진행 중이죠. 이미 싱가포르와 유럽연합은 도심지 터널의 대부분을 TBM으로 짓고 있을 만큼, 시공의 안정성이 입증된 공법이기도 합니다. 현대건설은 국내 최초의 TBM 터널인 ‘남산 1호 터널(1989)’를 시작으로 싱가포르, 베트남 등 국내외에서 26개 프로젝트를 진행하며 독보적인 시공 노하우와 기술력을 선보인 바 있습니다.
국내 최초의 한강터널 ‘김포~파주 2공구’, 왜 TBM을 적용했을까?
[ 현재 일산대교를 이용해 김포에서 파주까지 가려면 40분 이상 소요되지만, 터널이 완공되면 10분의 1 수준인 4분으로 단축됩니다. ]
현대건설이 시공 중인 ‘김포~파주 2공구’는 ‘수도권 제2순환고속도로’ 건설 구간 중 경기 김포시 하성면 마곡리에서 파주시 연다산동을 잇는 총연장 6.734㎞의 도로입니다. 최대 난코스는 한강을 가로지르는 2.98km의 하저 도로터널 구간으로, 한강 수면에서 20~35m 깊이에 시공됩니다.
현대건설이 이 구간을 교량이 아닌 터널로 짓는 이유는 무엇일까요. 이 지역은 위치상 군사분계선과 밀접해 있고, 멸종 위기인 수원청개구리와 천연기념물 재두루미의 도래지로 유명한데요. 지상으로 차가 다닐 경우 동물들의 터전이 위태로워 질 수 있는 점을 감안해 ‘터널’이라는 방법을 고안해 낸 것이죠. 그 후 전문가들은 상부의 흙 두께가 비교적 얕고 수압이 높은 복합 지반으로 이뤄진 것을 발견했고, 현대건설은 주변 환경과 조화를 이루면서도 안전한 터널 공법을 고민해 TBM 중에서도 ‘이수식 쉴드 TBM 공법’을 채택했습니다. 고수압·연약대층에서도 안전하게 굴착할 수 있고, 발파 공법에 비해 소음, 진동이 거의 없는 친환경 공법이기 때문입니다. 터널 굴착부터 벽면 조립, 토사 배출까지 모든 공정을 원스톱으로 처리할 수 있어 공기 단축에 효과적입니다. 특히 TBM은 작업자에게도 안전한 환경을 제공하는데요. 장비 내부에는 작업자가 대피할 수 있는 비상 챔버가 2군데나 있고, 비상시 이곳에선 72시간 동안 산소가 공급되게끔 시스템화되어 있습니다.
효율성과 안전성을 높인 터널 뚫는 자이언트 ‘두더지’ TBM
[ TBM 앞면 커터 헤드의 앞면에는 71개의 디스크 커터가 붙어 동심원을 그리면서 암반을 깎아냅니다. ]
현대건설과 한국도로공사는 ‘국내 최초 한강 하저를 횡단하는 도로터널 건설’을 기념하기 위해 전 국민을 대상으로 TBM 네이밍 공모전을 실시했는데요. 두 배 더 안전하게 지하터널을 건설한다는 의미를 담아 최종 네이밍을 ‘두더지’로 결정했습니다. 땅굴을 기가 막히게 뚫는 두더지는 TBM 기계와 많이 닮았습니다. 두더지의 강력한 앞발의 역할을 하는 부위가 바로 커터 헤드인데요. 커터 헤드의 앞면에 붙어 있는 71개의 디스크 커터가 동심원을 그리면서 암반을 깎아냅니다. 이 디스크 커터는 닳아 없어지면 헛돌아서 골고루 힘을 받을 수 없기 때문에 10~20mm 가량 닳으면 교체해 줘야 하는데요. 현대건설은 최첨단 기술인 대기압 커터 교체(Accessible Cutter Head) 시스템*과 디스크 커터 모니터링(Disc Cutter Rotation Monitoring) 시스템*을 활용해 교체시기를 관리하고 있습니다. 또한 보통 마모되는 디스크 커터를 교체하기 위해선 커터 헤드 뒤편의 고압 상태의 챔버(Chamber)*에 들어가야 했지만, 현장에 적용 중인 이수식 TBM 장비는 외부(일반 대기압)에서 작업을 진행할 수 있어 더욱 안전하고 편리합니다. 이밖에 ICT(Information and Communications Technologies, 정보통신기술)을 접목시킨 TBM 통합운전관리시스템(TADAS)으로 굴착 중 생성되는 지반 정보와 장비 상태를 실시간 파악하는 등 현장 관리의 효율성을 더했습니다.
*대기압 커터 교체 시스템: 커터헤드 뒤에 따로 공간을 만들어 작업자가 대기압 상태에서도 진입해 디스크 커터를 교체할 수 있는 장치
*디스크 커터 모니터링 시스템: 디스크 커터(면판) 회전수와 온도 정보를 실시간으로 모니터링해 교체 시기 및 비정상 마도 등을 관리할 수 있는 장치
*챔버: 굴진면을 지지하는 압력을 제어할 수 있는 공간으로, 평소 고압 상태로 유지하기 때문에 교체가 쉽지 않습니다.
[ 폭 2m, 두께 450mm의 세그먼트 10개가, 직경 14m에 달하는 링을 형성합니다(왼쪽). 세그먼트 조립기계 이렉터(Erector)를 이용해 레고처럼 터널을 만드는 모습. ]
무엇보다 TBM이 안전한 선진 공법으로 선호되는 이유는 굴진과 동시에 두꺼운 콘크리트 블록(세그먼트)을 레고처럼 조립해 터널 형태를 완성하기 때문입니다. 두 가지 과정이 동시에 이뤄지는 까닭에 안전하면서도 공기 단축에도 효과적이죠. 또한 여기서 나온 암반과 토사는 파이프를 통해 지상으로 배출, 모든 공정이 원스톱으로 이뤄집니다. 지상의 넓은 부지에 이수처리설비를 별도로 구축해야 하는 고가의 공법이지만, TBM이 세계적으로 인정받는 이유입니다.
축구장 길이를 훌쩍 넘는 초대형 기계…TBM 설치를 위한 2년여의 드라마
[ TBM 장비를 설치한 발진기지는 지하 9층 깊이, 폭 68m, 길이 320m에 달합니다. 터널의 시작점으로, 현대건설은 이곳에서 TBM의 조립을 마치고 굴진에 들어갔습니다. ]
현장에서 만나볼 수 있는 TBM 장비는 축구장 길이를 훌쩍 넘는 125m에, 아파트 6층 높이에 달하는 14m 직경으로 국내 최대 규모를 자랑합니다. 이 거대한 TBM 장비를 공수하고 설치하는 과정은 한 편의 드라마와 같았습니다. 세계 최대 TBM 장비 최대 제작사인 독일의 헤렌크네히트사가 제작 기간에만 1년. 그 후 총중량 3200톤에 달하는 초대형 장비를 국내로 반입하기 위해 140여 개로 분할한 다음 서해를 통해 국내로 들여왔습니다.
장비를 조립하기 위한 장소이자 터널 굴착의 출발점인 ‘발진기지’를 짓는 데도 대략 20개월이 소요됐는데요. 지하 9층 깊이, 폭 68m, 길이 320m의 발진기지는 웬만한 초고층 빌딩의 터파기 보다 규모가 큽니다. 현대건설은 이 초대형 발진기지에서 6개월에 거쳐 커터헤드, TBM 본체 장비의 조립을 마무리 지었습니다.
[ 마치 우주선을 영상 시키는 TBM의 내부는 소음, 진동, 분진 등이 적습니다. ]
스마트한 최첨단 기술로 더욱 안전하게 짓는 지하고속도로
현재 김포~파주 2공구 현장은 하루 평균 6m의 굴진을 하고 있습니다. 겨울철에 본격적인 굴진을 시작한 터라 장비 관리, 온도 유지 등 신경 쓸 것이 많지만, 과거에는 생각지도 못한 기술력 덕분에 안전하게 터널을 뚫을 수 있게 됐습니다.
굴진을 시작한 TBM 기기 내부는 거대 우주선과 닮아 있었습니다. 장비 운영을 위한 10여 명만이 남아 있는 공간은 터널 현장이라고 상상 못할 정도로 소음과 진동이 적었습니다. 또한 IoT 센서 부착, 스마트 태그를 통한 근로자 위치 관리 등 스마트 안전관리시스템으로 근로자의 안전까지 챙기고 있었는데요. 현존하는 국내 최고의 터널 스마트기술과 유례없는 규모의 TBM 장비 운영 등 역대급 터널 시공 현장을 벤치마킹하기 위해 동종업계 전문가들의 방문도 이어지고 있었습니다.
[ TBM 시공 경력을 보유하고 있는 글로벌 터널 전문가들이 함께 근무 중인 김포~파주 2공구. 각종 스마트 기술을 총망라해 근로자들의 안전을 먼저 챙기고 있습니다. ]
김포~파주 2공구의 안병철 현장소장은 “현장에 처음 온 분들은 일반 터널 현장과 달리 조용하고 진동·분진이 적어 놀란다”며 “굴착을 위한 장비 운영팀과 외부 지상팀, 현대건설 기술진까지 매일 약 200명의 인원이 국내 TBM의 새로운 역사를 쓴다는 마음으로 공사에 임하고 있으니 ‘국내 최초의 한강터널’의 탄생을 지켜봐 달라”고 전했습니다.
현대건설은 2024년 5월까지 17개월에 거쳐 상행선을 뚫고, 장비를 해체·조립 후 바로 옆에 하행선 터널을 1개 더 뚫을 계획입니다. 2026년 12월, 준공과 함께 제1외곽순환 고속도로 교통 혼잡은 물론, 수도권 서북측으로 접근성이 크게 향상되고, 일산대교를 이용해 김포에서 파주까지 40분 이상 소요되던 시간도 4분으로 단축됩니다. 10분의 1 수준으로 줄어드는 이동 시간에 지역 주민들도 손꼽아 공사가 마무리되길 기다리고 있는데요. 준공의 순간까지 현대건설과 ‘자이언트 두더지’ TBM이 펼칠 멋진 활약을 기대해 주시기 바랍니다.