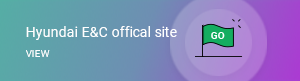
The landscape of Singapore is changing. Hyundai E&C has led such reshaping by carrying out the Changi Airport Reclamation Project and the Tekong Island Reclamation Project Phase 2, starting with the Pulau Tekong Reclamation Project in 1981. Following the reclamation work of Tuas Finger 1, which was completed last year, to the ongoing Tuas Finger 3 site, Hyundai E&C has expanded 7% of Singapore's land. Let us have a look at Singapore's Tuas Finger 3 reclamation site, where the sea is becoming the land and the shipping and logistics hub is being developed.
Singapore's Largest Undertaking of Manufacturing 227 Caissons
This is the Tuas region on the western outskirts of Singapore. Following the busy movement of dozens of dredgers, the blue sea is gradually turning into the land. It is the site of the Tuas Finger 3 reclamation work (hereinafter “Finger 3 site”), a third project of the “Tuas Mega Port Project” to build a total of four new cargo container terminals by reclaiming the sea. The Tuas Mega Port Project is a mega-development project that brings together container terminals distributed in southern downtown areas such as Pasir Panjang and Keppel to improve transportation efficiency and develop the city center.
Of the total volume of 65 million TEUs (1TEU = 20ft cargo capacity), the area of the Finger 3 site, which is responsible for 21 million TEUs, is 387ha, about 1.33 times larger than Yeouido. Hyundai E&C (35%), Japan's Penta-Ocean (35%), and the Netherlands' Boskalis (30%) will jointly carry out the manufacturing of 227 caissons, 25 million ㎥ of dredging, and 123 million ㎥ of reclamation. All the construction in principle should be jointly carried out by all parties, but each company is in charge of leading the construction which it has strengths in. Hyundai E&C, which already stands unrivaled in the field of caisson in Singapore, is leading the fabrication and installation of caissons.
[ On April 25, the site held a ceremony to commemorate the completion of the production of the 227 caissons. ]
A caisson is a hollow square concrete structure that is completely submerged in the sea and then filled with earth or sandstone to be used as the foundation of the bridge, breakwater, and inner wall. It is a large structure that is equivalent to one 12-story apartment building and requires high technical skills in construction because it is exposed to seawater. As many as 227 caissons will be installed at the Finger 3 site. If you connect them all, it is 9.1km, easily exceeding the height of Mt. Everest.
The site, which began construction in March 2018, began major works such as ▶ dredging and reclamation in June ▶ construction of access roads in August ▶ manufacturing of caisson foundation in October ▶ manufacturing of caisson in April 2019 ▶ installation of caisson in August 2021. The current process rate is 58.6 %, and the entire production of the 227 caissons was completed in April.
[ Dredging Work Using BD (Backhoe Dredger) ]
[ Reclamation Work Using TSHD (Trailing Suction Hopper Dredger) ]
[ PVD (Prefabricated Vertical Drain) for Ground Improvement ]
Manufacturing 227 caissons is the largest single project ever since Hyundai E&C entered the caisson market in Singapore in 1995. Despite the already highest level of construction capacity, the site constantly focused on addressing concerns and pursuing technology development to improve productivity. The idea born out of a collaborated contemplation of the staff and management was applied to the site after numerous trials and errors. This resulted in the feat of achieving productivity of up to 9.5 caissons per month and reducing the manufacturing period of 33 months calculated at the time of bidding to 3 months.
Consolidating Positioning in Maritime Construction with Unrivaled Technology
The site improves the speed of wall concrete placement by more than 40% compared to similar projects, and the productivity of manufacturing the first caisson is up to 30%. With these achievements, the site says, "This is the result of harmonious realization of Hyundai E&C’s original technology." In the implementation design, the length of the caisson was adjusted to reduce the number of manufactured caissons from 229 at the time of bidding to 227, and the process efficiency was increased by pre-manufacturing and assembling the reinforcement of the caisson’s base plate. In addition, by developing and introducing a quantitative measurement technique for measuring the hardness of concrete, Hyundai E&C shortened the manufacturing period while securing quality. Caissons are moved through a hydraulic transport device according to the manufacturing process, and the pump capacity was increased to improve the device transport speed by more than 60%, helping to reduce the time required for manufacturing. Technology derived from the passion of staffs and management has not only innovatively shortened the fabrication period but also became the basis for ensuring safety and quality.
In particular, the “Automatic Silane Coating Equipment Development” technology was recognized for its technical excellence and safety by winning the Gold Award, the highest honor in the construction sector, at the Workplace Safety & Health Innovation Award 2020 and the grand prize at the '2020 Hyundai E&C Innovation Awards'. The durability of concrete is more important for caisson, which is constantly exposed to seawater. Therefore, it is essential to coat silane that acts as a protective film on the concrete surface and prevents chloride from penetrating. The coating is done manually, and the caisson top used to be exposed to danger because workers had to climb high. To overcome this, the site developed an automated system that enables coating and maintenance while rotating under the injection pressure of the solution. Since it was possible to work by pressing a button on the ground, the site was able to fundamentally eliminate the risk of high-altitude work and exposure to chemicals, and secure a certain level of quality through automated operation.
The finger 3 site, which had been busy every day with constant technology development and perfect process management, could not avoid the impact of the COVID-19 pandemic. In particular, the caisson manufacturing operation is almost the only on-site construction that is manpower-intensive. It was not only difficult to manage nearly 1,000 foreign workers, but also challenging to operate the site due to strict quarantine and various regulations that lasted more than five months after Singapore’s lockdown. Given the nature of the 24-hour continuous production of caisson, day and night shifts was a must, but a series of challenges persisted due to the lack of manpower. As a countermeasure, the site not only thoroughly managed working hours by actively reflecting alternative holidays due to overtime, but also efficiently deployed skilled workers, provided incentives to remaining workers, doing its best to run the site smoothly. All the employees were united, so even in an unprecedented emergency, the manufacturing of caissons could be completed as planned, without a single major accident.
If you look at the satellite map of the western sea of Singapore, you can have a glimpse into the moments of the hectic site. At the heart of the inner wall blocking the water path and the land gradually filling up, you can feel the valuable sweat shed by all staffs and management. Today, we have more way to go than traveled. The joy of completing an important process is brief, as the site continues to remain committed to perfectly completing the project.
How Are Caissons Manufactured and Installed?
Caisson fabrication can be largely classified into two types: “caisson manufacturing" taking place on the ground and “caisson installation" taking place on the sea. First of all, caissons are fabricated at the manufacturing site, which is carried out 24/7 sequentially. It takes 78 to 83 hours (depending on the type) to place one unit of caisson, which cannot be stopped once it starts.
When a huge caisson is completed at the manufacturing site, it is carried to the sea in a 20,000-ton floating dock owned by Hyundai E&C. Hyundai E&C is the only Korean builder that owns more than 20 large marine equipment needed for port construction, which adds to the company’s competitiveness in. When the caisson arrives at the launching site in the middle of the sea, the floating dock is filled with water and submerged, and the caisson is pulled out by a tugboat. The process takes about seven hours. After that, the tugboat is moved to a predetermined location, and then the caisson is permanently installed with a barge built for installation.
① Foundation Placement
② Wall Structure Placement
③ Silane Coating
④ Floating Dock Loading
⑤ Launching
⑥ Transportation
⑦ Installation