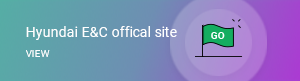
Constructions can be found everywhere in our lives, such as houses for comfort, roads and bridges for mobility, and power plants for electricity. Therefore, Hyundai E&C has placed safety as its top priority for management this year so that the spaces it constructs can be offer precious and happy experience for people. It aims to strengthen what has been good so far and boldly apply new systems. Here’s closer look into Hyundai E&C’s safety, getting better day by day.
Hyundai E&C’s safety management has become more systematic and solid over the years. The global builder elevated its Safety Support Office to Safety Management Headquarters following a corporate reorganization in October last year, consolidating its commitment to occupational health & safety (OSH) management. In addition, it has made site safety managers full-time and expanded its pool of heavy equipment experts. In addition to making it mandatory for office workers to acquire construction and industrial safety qualifications, a training program has been developed to strengthen the safety capabilities of executives and employees. Hyundai E&C which strengthened its safety organization and laid the foundation for OSH management, is renewing its commitment to safety by ▶ spreading worker-centric OSH culture ▶ expanding investment in safety systems ▶ and implementing a smart safety management. The business headquarters and safety management headquarters plan to work together to achieve ‘ZERO serious disaster’ across all sites..
‘Right to Suspend Work!’: Towards Safer Culture for Employees
What if there is a construction site that compensates for wages even if you leave work early due to your poor physical or mental condition? This may sound odd, but it is possible at Hyundai E&C. As construction workers age day by day, the risk of occupational accidents due to health problems cannot be ruled out. Smart construction technologies are being developed, but they are insufficient to replace 100% the know-how of skilled workers. Accordingly, Hyundai E&C has been implementing industry's first ‘Right to be Excluded from Work’ system since November last year to prevent industrial accidents by excluding those who complain of health issues and symptoms from work in advance. Daily site workers may request their work leaders or site supervisor to exclude them from work during a Tool Box Meeting (TBM). A sudden deterioration of physical and mental condition may occur during work. If so, the worker scan the QR code of the [Safety e-Report] attached to the safety helmet and make an ‘emergency call.’ Upon request, the worker will be excluded from work after meeting with the Hyundai E&C safety and health manager and the manager of partner company. Once the worker recovers as deemed by the worker and the partner company, he or she can rejoin the work site. In order to align the system with reality, Hyundai E&C promised to guarantee the right to be excluded from work only for the same day's work and to compensate for the loss of wages for the remaining working hours. It also banned disadvantages of personnel management when subject to this system.
The ‘right to work suspension’ that allows ‘any’ worker on site to refuse working in an unsafe environment has become widely exercised. Hyundai E&C is actively promoting the right to suspend work as a natural right of workers on construction sites. Workers can request the right to suspend work through the [Safety e-Report] in the following cases: ▶ non-installation of safety facilities ▶ unavailability of personal protective equipment ▶ exposure to risks of fire, explosion, suffocation, addiction ▶ exposure to risk of falling or collision ▶ non-installation of protection system▶ use of defective work plate and ▶occurrence of physical and mental problems.
In addition, ‘smart learning for safety management’ has been expanded so that all site managers and workers can enhance their safety capabilities. Furthermore, OSH training videos were produced in Chinese, Vietnamese, and Myanmar for growing number of foreign workers, and qualification tests are conducted for signal man, safety guards, rope operators and mobile elevated work platform operators.
‘Win-Win Cooperation!’: Paradigm Shift of OSH System
Hyundai E&C is operating various systems to strengthen the safety capabilities of its partners who are also responsible for site safety. Daily Activity Briefings (DABs) is a daily safety inspection meeting with partners. The meeting, checking today’s safety management record and identifying high-risk operations and sharing tomorrow's work plans and precautions, is held across all Hyundai E&C sites.
‘ZERO Serious Disaster’ is possible only when both the builder and its partner are safety-aware. To this end, Hyundai E&C tripled its weighting of safety score from 10% to 30% when evaluating the performance of its partners. Safety standards have been drastically enhanced by canceling the registration of partner companies if certain scores are not met, and restricting new registrations and bidding participation for companies that are not eligible for safety. In addition, partners that cause a serious accident due to negligence in management will be subject to ‘one strikeout’ system.
A system has also been set up to encourage safe site management to become the growth driver of partners. Incentives have been greatly expanded by increasing the amount of rewards to 500 billion won for partners excelling in site safety management. Hyundai E&C also introduced a ‘50% advance payment system for safety management fees’ to help its partners take care of safety measures starting from the site preparation stage. The system reduces the cost burden on partners by paying 50% of the OSH costs under subcontracts first. In order to prevent safety accidents that may occur in the gray zones at the site in advance, a separate safety budget other than statutory OSH management expenses will also be provided.
In addition, safety consulting from external professional service providers is provided free of charge to small and medium-sized partners. For those in blind spots not eligible for mandatory hiring of OSH manager (small construction with a contract amount of less than 10 billion won), additional wages of 4 million won per month will be provided in addition to the contract amount when hiring a safety manager. As such, Hyundai E&C plans to create healthy and safe sites with its partners in the future.
‘Keeping Sites Smart’: OSH Management Applying Digital Technology
Hyundai E&C is developing a digital safety technology tailored to its needs. ‘Disaster Prediction AI,’ rolled out in October last year, provides disaster risk information of domestic projects to sites every day. It is a proprietary system created by collecting some 40 million big data from various projects conducted over the past decade, and site managers analyze the planned construction information entered into the site management system to derive the probability of safety accidents and safety management guidelines for each type. The site supervisor and managers can preemptively manage safety by receiving disaster prediction information through e-mails and text messages on the day of work.
The ‘AI Image Cognitive Equipment Stricture Prevention System’ is a digital technology that eliminates blind spots at construction sites. The system automatically distinguishes objects from people using cameras installed on the side and rear of heavy equipment. It is a technology that can secure the safety of workers by giving off an alarm when approached by a person and is also equipped with a state-of-the-art ICT (Information and Communications Technology) system.
‘The Integrated Smart Automatic Measurement Monitoring System’, developed for the first time by a Korean construction company, is also playing a crucial role in terms of site safety management. It is integrated with the IoT-based site safety management system 'HIoS', which is a industry’s first proprietary system developed in 2019, tasked to prevent collapse accidents, allowing for a real-time integrated management of temporary structures and ground conditions. In addition, Hyundai E&C is fully committed to innovating safety culture through smart construction technology such as a ‘Remote Site Management Platform’ that enables three-dimensional site management by connecting unmanned drones, 360-degree cameras, and smart glasses for the first time in Korea.
Safety Rewards Cash Points? Zero-Disaster Incentive System: ‘H-Safety Wallet’
Caring for people and keeping sites safe will help you earn Naver points! For construction sites to be safely completed without any serious disaster, safety awareness of every worker is essential. Hyundai E&C is the first Korean builder to develop an ‘H-Safety Wallet’ so that workers can further commit to safety. It is a ‘Disaster-Free Incentive System’ that provides points in proportion to the number of working days without accidents, which can be used like cash. Points will be accumulated as benefits for zero disaster work, and you can even earn points by watching safety-related education videos or make suggestions or reports on safety. However, in the event of a disaster, the cumulative points are maintained, but the weighting is initialized. Hyundai E&C, which began developing the ‘H-Safety Wallet’ platform in July last year, plans to introduce it to all domestic sites in the first quarter of this year after design work and consultation with Naver.
[ H-Safety Wallet ]